After water, concrete is the most abundant resource in the world – or to put it another way, the most used man-made material on the planet.
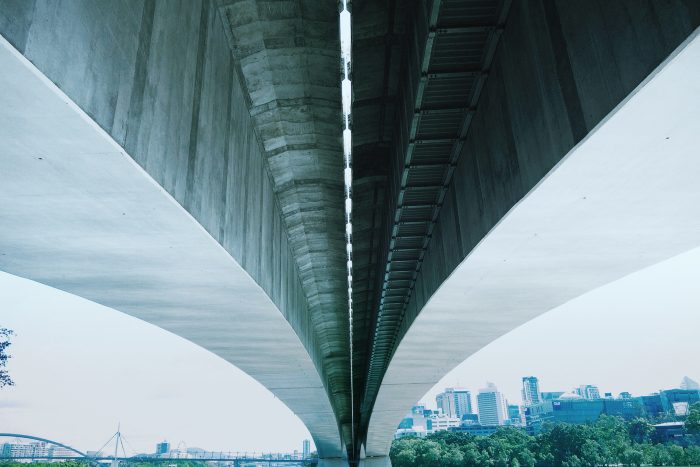
Concrete is fundamental in shaping our world. That’s because of its inherent benefits of strength, durability, resilience, safety and affordability to create vital infrastructure – roads and railways, homes, offices and the cites we live in.
Concrete is crucial for the transition towards global sustainable development and more generally for the infrastructure to support clean energy development. Concrete also plays a significant role in the energy efficiency of buildings.
But what about Cement? Cement and Concrete are intertwined in the minds of many people, but also in actual fact. Concrete is the material that we interact with every day – in the structure of our homes, offices and hospitals, supporting our bridges and infrastructure, laid on our roads and pavements. Cement is the vital glue that binds the ingredients of concrete together and makes concrete the truly versatile and beautiful building material that is solving the needs of the world today and the challenges of tomorrow.
The Global Context
According to the United Nations 68% of the world population are projected to live in urban areas by 2050.
As the world continues to urbanize many countries will face challenges in meeting the needs of their growing urban populations, including for housing, transportation, energy systems and other infrastructure, as well as for employment and basic services such as education and health care.
- Cement in brief
-
Cement’s central use is to bind together the ingredients of concrete – sand and aggregates. Cement is a glue, acting as a hydraulic binder, meaning it hardens when water is added. Cement itself is a fine powder that is made by first crushing and then heating limestone or chalk, with a few other natural materials, including clay or shale, added. The ground base materials are heated in a rotating kiln to a temperature of up to 1,450 degree C or as hot as volcanic lava.
- Concrete in brief
-
Concrete is a mixture of cement, water and aggregates (e.g. sand and gravel, crushed stone or recycled concrete) and often includes small amounts of admixtures. The exact ratios and mix, and type of aggregate use depends on how the concrete is intended to be used. One of concretes key assets is its versatility which means concrete can be used in a variety of ways to solve the many needs that individuals and societies have – shelter, housing, providing clean water and sanitation, transport, business and commerce. Concrete is an extremely strong, durable and resilient material.
- Looking back and now
-
Cement and Concrete have a long history of use in our world.
The Roman Empire accelerated the use of concrete. Some of its most famous buildings still stand today including the Roman Pantheon (which remains the largest unreinforced concrete dome in the world) and the Coliseum. Both of these buildings, built around 2,000 years ago, demonstrate the resilience and durability of concrete. Although the cement that was used was different to today’s cement material – the principle was similar.
Today Portland clinker based cement is the most common type of cement in use. Portland cement was first developed in the beginning of the 1800s. All member of the GCCA are Portland clinker based cement producers.
- How is cement made
-
Below we outline the very basics of what is involved in the manufacture and production of cement. Our affiliate organisations across the world have many comprehensive descriptions, with an array of infographics, videos and different languages.
You can visit them here at:- Cámara Nacional del Cemento (Mexico)
- CEMBUREAU (the European Cement Association)
- Cement Association of Canada
- CMI (Ireland)
- Federación Interamericana del Cemento (FICEM) (Latin-American Region)
- Mineral Products Association (United Kingdom)
- Portland Cement Association (USA)
- SNIC/ABCP (Brazil)
- Union of Cement Producers – Soyuzcement (Russia)
Cement production – the (very) basics
- Step 1: Find a location where limestone is plentiful. Thankfully, much of the earth’s crust has limestone near the surface and means there is a plentiful supply. It also means that cement manufacture is mostly a local industry, produced close to where it is needed.
- Step 2: Extract the limestone from a designated quarry. Quarries today are managed to rigorous standards and many have detailed plans in place for land use and habitat management to ensure they are returned to support diverse plant and wildlife.
- Step 3: Crush the limestone rock. Health and safety policies at quarries and indeed cement plants, and right across the production and construction chain are first and foremost in cement companies’ priorities. All GCCA members have rigorous policies in place.
- Step 4: Add other ingredients to the crushed limestone such as clay or shale – grind and mix together. Cement production is all really about chemistry. Although the process sounds simple the chemistry of the raw materials and the subsequent mix is very carefully monitored and controlled.
- Step 5: Put the mix into a giant rotating kiln and heat up to 1,450 degree C. Over a period of about 30 minutes a chemical process takes place which releases the C02 from the crushed rocks. Cement producers have been working hard on reducing greenhouse emissions both in the energy that is used to produce cement and looking at ways of reducing the overall emissions. There are many innovations and different methods of working to reduce the overall carbon footprint in cement production and concrete use. Kiln technology has improved significantly in recent years to ensure that the heat produced is maximised and the fuel that heats it is minimised within the process. Also, later down chain, did you know that concrete naturally re-absorbs CO2 from the atmosphere – so with good design, buildings can be an effective carbon store.
- Step 6: The heating process and the resulting chemical reactions lead to the formation of the material that in the industry is referred to as ‘clinker’. This has the property of binding concrete ingredients together through (what is scientifically referred to as) its hydraulic properties. All GCCA members are clinker producers. Once cooled, the small round clinker forms are ground down again to a fine powder and number of specific ingredients, such as gypsum, are added in small quantities and depending on the required intended application of the cement or how long drying time is required. Cement may also be mixed with other finely ground minerals such as slag, fly ash, limestone or other materials (which mostly come from the by-waste of other industries) to replace part of the clinker, thereby often achieving a significant reduction of the CO2 emissions.
- Step 7: You now have cement. As a producer you might bag it up for the construction sector and wholesale trade, or transport it in bulk to concrete plants who will mix the cement with aggregates to make concrete. Most cement is transported locally – which avoids unnecessary and long miles of transportation on roads and global shipping.
- Properties of Concrete
-
Non-flammable – Concrete does not burn: providing fire safe structures
Rust-resistant – Concrete does not rust: providing low maintenance
Rot-proof – Concrete does not rot: reducing risk of unseen damage
Insect-proof – Concrete does not suffer from insect damage: reducing risk of unseen damage
Flood-resilient – Concrete does not swell and warp when wet: providing resilience to flooding and internal water damage
No emissions – Concrete does not emit volatile organic compounds (VOCs): these are an issue with other building materials and impact health
Water-safe – Concrete is inert: it can be used to store and supply clean drinking water
Heat-reflective – Concrete has high albedo: the light-coloured surface of concrete reflects heat whereas dark surfaces like asphalt absorb heat and cause the problematic urban heat island effect
Water-permeable – Concrete paving can be permeable to water: when it rains water can permeate through to reduce surface flooding
Vehicle emission reducing – Concrete paving is stiff and rigid: vehicles have lower emissions on rigid roads
Thermal mass – Concrete has thermal mass, like stone and masonry, which can be used by designers to reduce energy demand.
Range of Densities Possible – Concrete can be made in a range of densities from lighter than water (10kN/m3) to heavy concretes (30kN/m3) that are used in hospitals to absorb radiation: typical concrete density is 23kN/m3
Compressive strength – Concrete has compressive strength: strengths from 5MPa (economic low strength masonry) to 80MPa (high rise buildings) and can be designed to have more than double this strength for ultra high performance
Tensile strength – Reinforced Concrete has tensile strength: concrete is compatible with reinforcement steel which provides tensile capacity and together they make the most widely used composite material in the world
Available & Affordable – Concrete is locally produced. It is widely available and suitable to build at a reasonable cost, without compromising on quality and strength and with low maintenance costs
Recyclable – Concrete is one hundred percent recyclable. All its components are recyclable which can support a circular economy
Whole-life benefits – Taking a whole-life cycle performance into account, concrete has a low carbon footprint thanks to its durability, to its thermal mass effect, to its recyclability and to the carbonation of cementitious materials.
- Glossary
-
Alternative fuels and raw materials (AFR):
Waste materials used for co-processing are referred to as alternative fuels and raw materials (AFR) (see Co-processing).
Aggregates
Aggregates for concrete comprise small stones, gravel and sand.
Best practices
A best practice is a method or technique that has been generally accepted as superior to any alternatives because it produces results that are superior to those achieved by other means or because it has become a standard way of doing things, e.g., a standard way of complying with legal or ethical requirements. GCCA is developing best practices documents for its members as to demonstrate industrial leadership in cement manufacturing.
Biodiversity
Biodiversity refers to the variety of plants or animals in a particular area. In the cement and concrete sector it is usually used in relation to quarries (see Quarries Rehabilitation).
Built environment
Built environment encompasses all buildings and man-made infrastructure such as rail and road transport; ports and airports; water supply, collection and flood defences; energy generation, storage and distribution.
By-products
By-product is a substance, resulting from a production process, the primary aim of which is not the production of that item. The cement and concrete industries use by-products from other industries such as slag from the steel industry and fly ashes from coal fired power plants.
Carbonation
Cement recarbonation or concrete carbonation refers to the process where CO2 is absorbed by concrete during its use and end-of-life phase. The amount absorbed is significant but less than the total emitted in cement production (see Recarbonation).
CCUS (Carbon Capture Use and Storage)
Carbon capture, utilization and storage (CCUS), also referred to as carbon capture, utilisation and sequestration, describes processes that capture CO2 emissions from industrial sources and either reuses or stores it so it will not enter the atmosphere.
Cement
Cement is a powdery material which mixed with water, sand and gravel will form concrete and mortar when mixed with water (see Clinker, Concrete).
Circular economy
The concept of a circular economy has to be seen as a ‘system’, opposed to the traditional linear economy. Circular economy means aiming at minimising waste and making the most of resources. It also means designing for circularity.
Clean energy
Clean energy is synonym to renewable energy. It refers to energy sources such as wind, hydro, solar, geothermal energy as well as energy from biomass (see Renewable energy).
Climate change
Climate Change is a concept which designate both global warning and its effects (see Global warming).
Climate mitigation
Climate change mitigation designates the actions to limit the magnitude or rate of long-term global warming and its related effects. It include mitigating emissions and adapting to the consequences of climate change.
Clinker
Clinker is a nodular material produced made by heating limestone and clay at a temperature of about 1400 °C – 1500 °C. It is the basic ingredient of cement, the one which confers hydraulic properties to cement. (see Cement, Concrete, Limestone).
Clinker substitutes
Clinker substitutes are alternative materials to clinker in cement production. The use of clinker substitutes is one of the main lever for the reduction of CO2 emissions related to cement manufacturing.
CO2
CO2 stands for carbon dioxyde. It is a colorless, odorless, and non-combustible gas. It is a greenhouse-gas that contributes to global warming. Formed by complete combustion of fossil fuels (coal, charcoal, natural gas, petroleum) and CO2 containing products (such as limestone), it is released also through living organisms respiration and by the gradual oxidation of organic matter in soil.
CO2e
Greenhouse gas emissions expressed as an equivalent CO2. For example, methane greenhouse gas potential is many times higher than carbon dioxide, but for simplicity all the equivalent emissions are expressed in terms of CO2. Often it is simply described in shorthand as CO2: it is critical to ensure that the more rigorous CO2e is being reported/compared even if the shorthand is used (see CO2, greenhouse gas).
Concrete
Concrete is a building material, the most man-made used substance after water. Concrete is made of cement, sand, aggregates, water and admixtures. It is initially malleable in its “wet” state and solidifies over time, gaining strength and durability (see Clinker, Cement, Aggregates, Admixtures).
Co-processing
Is a term that refers to the use of waste as a source of energy or raw material (or both) to replace fossil fuels such as coal, petroleum and gas (energy recovery) and natural mineral resources (material recycling) in industrial processes such as cement production. Waste materials used for Co-processing are referred to as alternative fuels and raw materials (AFR).
Durability
Durability describes how a material resists mechanical or chemical degradation.
Embodied CO2 ( ECO2e)
The CO2e arising from the whole life of a material/project. It is critical that the whole life is considered. It is critical that when comparisons are made between materials and products that there is functional equivalence (for example same service life) and the same rules are applied in determining the embodied CO2 (for example what is and is not included).
Environmental Product Declaration (EPD)
An independently verified and registered document that communicates transparent and comparable information about the life-cycle environmental impact of a product.
Operational CO2
Operational CO2 (or more correctly ‘Operational CO2e’) is the carbon dioxide (or more correctly, all greenhouse gases expressed as equivalent CO2) that are caused by the operation of a building or infrastructure.
Geopolymers
A term commonly used to describe alkali activated binders. Until now, alkali activated binders have been produced mostly for demonstration purposes and have only been used in non structural applications e.g. paving. Up to 90% CO2 emissions reduction compared to Portland cement is postulated but this does not take into account emissions due to the production of the activators. So based on today’s knowledge, the reduction potential of materials like slag or fly ashes as clinker substitute in blended cements seems to be more efficient than the use of alkali activated binders.
GNR
“Getting the Numbers Right” (GNR) or “GCCA in Numbers” is a voluntary, independently-managed database of CO2 and energy performance information for the global cement industry. The database delivers uniform, accurate and externally-verified data so that the industry and its stakeholders can understand the current performance and future potential.
Greenhouse gas
A greenhouse gas is a gas that absorbs and emits radiant energy within the thermal infrared range (see CO2, CO2e).
Global warming
Global warming is a long-term rise in the average temperature of the earth climate system. Global warming and climate change are often confused but in fact climate change is a broader term as it includes both global warming and its effects such as extreme weather events and changes in precipitation (see Climate change).
Infrastructure
Rail and road transport; ports and airports; water supply, collection and flood defences; energy generation storage and distribution (see Built Environment).
Hydraulic properties
The term hydraulic proporties is used to describe a the fact that when mixed with water, cement reacts chemically and becomes hard and strong. Cement is categorized as either hydraulic or nonhydraulic, depending on how it mixes with water. Nonhydraulic cement does not harden underwater or in damp conditions. Certain chemicals are added to make hydraulic cement.
Innovation
Innovation is a “new idea, creative thoughts, new imaginations in form of device or method”. GCCA’s mission is to drive, support and advocate innovation in the cement and concrete sector to improve its sustainability and in particular lower its CO2 footprint in particular facilitate research and develop partnership with key stakeholders (including for research, funding and advocacy).
Limestone
Limestone is a sedimentary rock mainly composed of calcium carbonate. This is why when heated it releases CO2. It is the main raw material used in clinker production. Limestone is the main raw material used in cement production (see Clinker, CO2).
New binders
New binders or novel cements is a term used to designate alternative to traditional Portland clinker based cements. Those are binding materials manufactured using novel, low-carbon processes that offer similar performance to traditional cement. Most react in a familiar way with water, but some react with CO2 to solidify into a hardened mass (see Clinker, Cement).
Novel cement see new binders
Occupational health
Occupational health is the branch of medicine which deals with the prevention and treatment of work-related injuries and illnesses.
Quarry
A quarry is an open surface where stone, rocks, construction aggregate, sand, gravel, clay limestone is excavated from the ground.
Raw materials
A raw is a primary basic material, unprocessed, or commodity used in the primary production or manufacturing of good. Cement and concrete industries main raw materials are limestone, clay, sand and aggregates. Those are also sometimes called feedstock.
Recarbonation
Cement recarbonation or concrete carbonation refers to the process where CO2 is absorbed by concrete during its use and end-of-life phase. The amount absorbed is significant but less than the total emitted in cement production (see Carbonation).
Rehabilitation
Rehabilitation of a quarry is the action of restoring a usable habitat for ecosysten when the quarrying operation is finished. The cement industry would in most case operate rehabilitation by extraction zone.
Renewable energy
Renewable energy is energy that is produced from renewables sources (naturally replenished on a human scale) such as energy from wind, hydro, solar, geothermal, tide, waves and biomass.
Resilience
The ability to deal with stress accumulation on a system or a shock event such as natural disaster, accident or malicious attack.
Safety
Safety at work describes policies and procedures in place to ensure the safety and health of employees within a workplace. Ensuring healthy and safe working conditions for employees and contractors is the most important priority for the cement and concrete industry and its broader value chain. We are committed to strive to achieve zero harm for employees contractors and everyone that come in contacts with its business. Everyone has a right to go home safe and healthy at the end of every day.
Sustainability
Sustainability is the concept of meeting the needs of today without compromising the ability of future generation to meet their needs. It is composed of three pillars: economic, environmental and social sometimes informally called triple bottom line and known as profits, planet and people. GCCA is working on concrete triple bottom line.
Thermal mass
Thermal mass is a material property. It is the ability of a material to absorb, store and release heat energy. It is measured in W/m2/K. The higher the thermal mass, the larger the energy absorbed/released per unit area per degree Kelvin temperature difference between the internal temperature and the temperature of the material (see Thermal Insulation, Thermal Decrement).
Thermal decrement
Thermal Decrement describes the effect of thermal mass on energy transferred through a wall when the external and internal temperatures are not constant. When the outdoor temperature cycles above and below the indoor temperature in a 24 hour period the thermal mass enhanced effect means a heavyweight wall can thermally outperform a lightweight wall with the same steady-state thermal insulation value.
Thermal insulation
Thermal Insulation is measured in W/m2/K. The better the insulation the lower the energy that is transferred across an external wall/roof/floor per unit area per degree Kelvin temperature difference between inside and outside. If the temperature difference is doubled, so is the energy transferred. Thermal insulation values are based on a steady state temperature difference between inside and outside (see Thermal Decrement).
Urbanisation
The increase in habitation of cities as a percentage of total population.
Value chain
A value chain is used to describe the system which include the full range of activities – including design, production, marketing, distribution and use, linked to a particular business. In the case of cement and concrete, the whole value chain included raw materials quarrying, energy supply, production and use, design, buildings contractors and architects, buildings users and end of life actors. A high-level model developed by Michael Porter used to describe the process by which businesses receive raw materials, add value to the raw materials through various processes to create a finished product, and then sell the finished product to customers.
Whole life
Whole life (see also cradle-to-grave) describes all stages in a product or project life from material sourcing to end of life prior to second life. It includes sourcing, processing, manufacture, construction, use, maintenance, re-use, demolition and processing for second life as well as transport impacts. In the case of biogenic products it includes release of carbon dioxide or methane arising from combustion or landfill.
Waste
A waste is a substance or an object which its owner discards, intends to discard or is obliged to discard. Waste can be re-used, recycled or recovered. This is the concept of a circular economy (see Circular Economy, Alternative Fuels and Raw Materials).