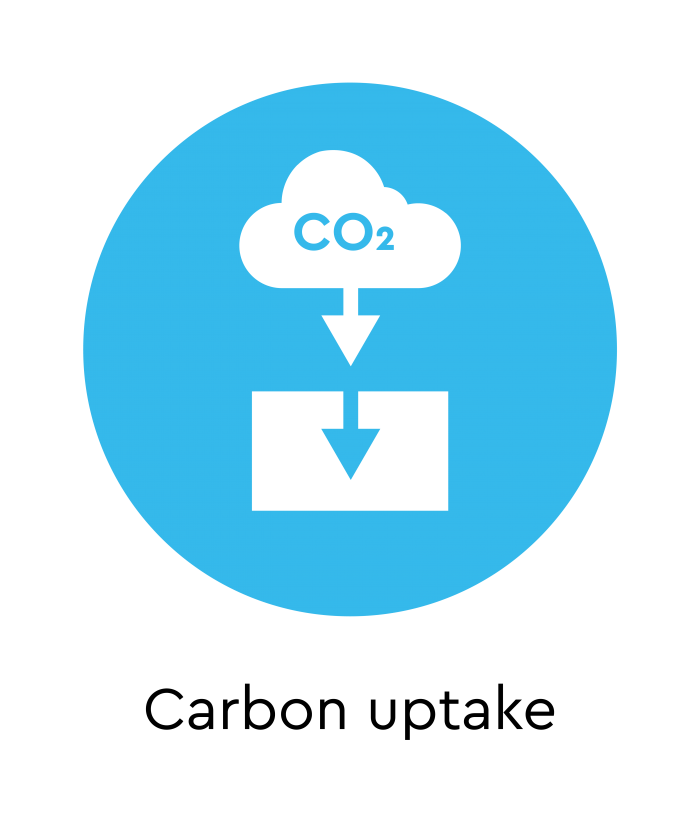
Everyone knows that making cement produces CO2. But did you know that concrete reabsorbs a significant amount of that CO2 over its lifetime in a process known as carbon uptake or recarbonation?
It is well-known that concrete is responsible for significant CO2 emissions, primarily as a result of the carbon-intensive process by which its key ingredient, cement, is manufactured. What is less well known is that concrete absorbs CO2 throughout its lifecycle, a property known as cement recarbonation, concrete carbonation or, more simply, carbon uptake.
Recarbonation is a natural process, occurring when concrete reacts with CO2 in the air. The exact amount of CO2 that concrete can reabsorb has a maximum of 100% of that emitted during the calcination of limestone in the cement manufacturing process. (These are known as process CO2 emissions and are the cause of approximately 60% of the embodied CO2 of concrete.) The actual amount of carbon uptake will depend on a range of parameters including the resistance class, exposure conditions, thickness of the concrete element, recycling scenario and secondary use. A practical estimate of the global carbon sink provided by all concrete is 25% of the process CO2 emissions released during cement production.
The carbon uptake process also happens at different speeds, occurring relatively quickly in non-reinforced products or thin/porous applications (renders, mortars, concrete blocks and mineral foams), but more slowly in reinforced concrete and thicker elements. Non-reinforced porous applications, such as masonry, that are exposed to air, can fully recarbonate within a few years, and it is estimated that such applications account for about two-thirds of the concrete global carbon sink.
Another significant portion of concrete carbon uptake occurs when reinforced concrete structures are demolished, as the increased surface area and exposure to air accelerates the process. The amount of carbon uptake is even greater when stockpiles of crushed concrete are left exposed to the air before reuse.
Finally, several carbonation-based binders have emerged, which are not only produced with lower CO2 emissions (burnt at lower temperature) but mostly use a significant amount of CO2 to harden. Such applications are however currently limited to niche markets.
Header photo by Paul Mocan on Unsplash