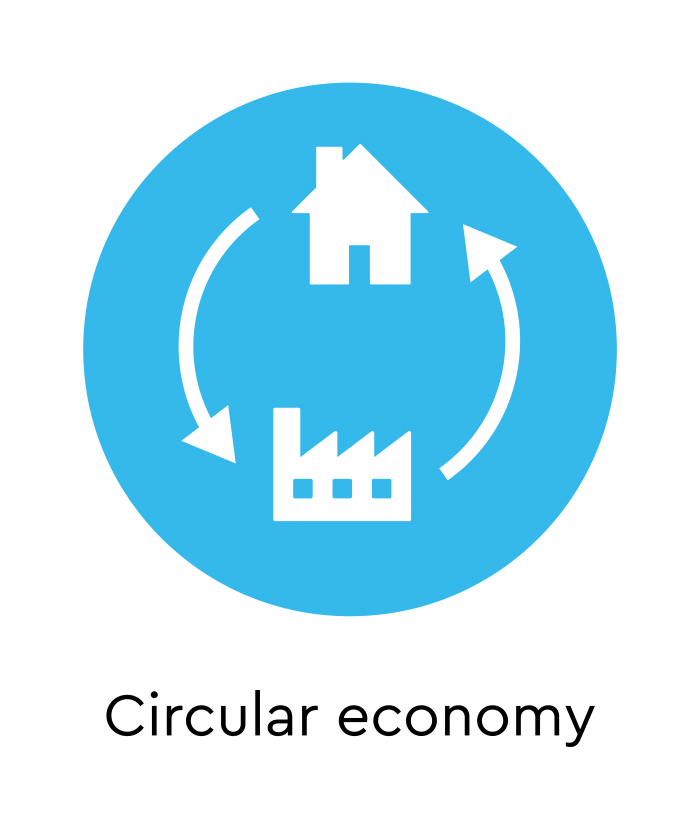
The concrete and cement industry is a key link in the circular economy, utilising recycled/secondary aggregates and cementitious industrial byproducts in concrete and alternative fuels/raw materials in cement kilns.
Concrete is durable: buildings can be reused and repurposed long after original design life has expired, maximising use of resources and slowing the circular economy loop. Concrete’s durability also makes it ideal for design for disassembly. Elements can be designed for recovery and reused in new projects. At end of life, if reuse, repurpose or disassembly are not feasible, concrete demolition waste can be recycled as an aggregate, reducing both the extraction of new raw materials and the amount of waste sent to landfill.
Circular economy and industrial ecology principals have been applied by the cement and concrete industry for decades, utilising the by-products of other industries and various other secondary materials, including municipal refuse and concrete demolition waste.
Supplementary cementitious materials (SCMs) and alternative fuels/raw materials
It is commonplace to use SCMs, often by-products from other industries, such as fly ash from coal fired power stations and ground granulated blast furnace slag (GGBS) from iron ore production, to partially replace clinker in cement or directly in concrete. Typical replacement rates are 30% to 50%. For some applications, the properties of the concrete are usefully enhanced by these by-products, which are otherwise often landfilled.
Similarly, alternative fuels derived from industrial by-products and waste materials, including municipal refuse, can be used as a partial substitute for traditional fossil fuels, such as coal and petcoke, in the cement kiln. Co-processing reduces the use of more carbon-intensive fuels, as well as contributes to the circular economy, making use of materials otherwise destined for landfill. In addition, some alternative fuels, such as used tyres, contain elements required in clinker production, helping to reduce raw material consumption.
Design for disassembly
The aim of design for disassembly (DfD) is to aid deconstruction (demolition) through planning and design. It allows components and materials to be removed more easily, facilitating their subsequent reuse. In this way, DfD provides economic and environmental benefits to builders, occupants, and communities. It also helps to reduce the consumption of raw materials, as well as lowering waste during construction, renovation, and demolition. Concrete’s durability, mechanical and fire resistance, global availability, variety of type and form, and flexibility in design and application, give it significant potential for disassembly and reuse.
Recycled aggregates
The availability of naturally occurring virgin aggregates varies from country to country and region to region. Typically, with adequate planning by the relevant government authority, the available resources will be accessible; however, when possible, use of recycled material should be considered. In addition, many areas with mature infrastructure are faced with an increasing amount of construction and demolition waste. There is therefore increased interest in recycled aggregates with concrete demolition waste a major source of such materials.
Recycling rates for crushed concrete vary significantly, depending on local laws/regulations for landfilling demolition waste and accessing natural aggregates. Where there are incentives and/or penalties, the aggregates industry has adapted to increase the use of recycled concrete as a source of aggregates. Policies that require the segregation of good-quality concrete waste during demolition processes, as well as to maintain its traceability, also help to maximise the re-use of recycled concrete aggregate. High re-use rates are reported in Netherlands, UK and Japan.
Recycled concrete is primarily used for road construction, with smaller amounts also used in new concrete production. When used in concrete production, concrete quality can be maintained at levels the same as that of concrete made with virgin aggregates by optimising the mix design (typically, recycled aggregate is restricted to 20% of the aggregates). Concrete production may also require slightly higher cement contents when recycled aggregates are used.
The use of recycled concrete aggregates is a clear and obvious example of the circular economy at play and has benefits that include reducing the use of natural resources and reducing landfilling. It provides significant opportunity for the concrete industry to contribute to the sustainability of the modern built environment.
Further reading and sources:
Design for Disassembly
Header photo by Paul Mocan on Unsplash