Mineral Products Association trials of calcined clay in cement could reduce carbon by up to 40 per cent
A new project trialling the use of calcined clay in cement and concrete manufacture could lead to carbon savings of up to 40 per cent and a more sustainable use of resources, if implemented across the UK.
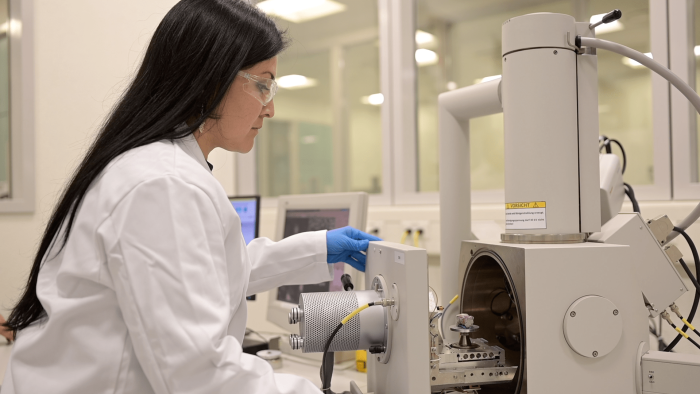
The Mineral Products Association (MPA) has been appointed lead partner for the research, which will demonstrate how calcined clay can be used to both utilise by-products from other industries and create low carbon cements.
Funded by an Innovate UK grant award, the two-year project will use two main sources of clay materials – one arising from overburden at mineral extraction sites and another from brick manufacturing. Calcined clays from these sources have the potential to divert 1.4 million tonnes of material from potential waste streams and cut the embodied CO₂ of cement by an expected range of 20-40 per cent, compared to the market leading CEM I cement.
Using clay also requires less, or in some cases no heating (for example when using waste brick) when compared to cement clinker production.
Clay is a naturally abundant material in the UK, which can offer an alternative to other industrial by-products, including ground granulated blast-furnace slag (GGBS) and fly-ash which are being successfully used to lower embodied carbon within cement.
Two heating methods are being trialled to prepare the clay for use in cement and concrete. These are a rotary kiln, a commonly used technique, and innovative ‘flash heating’.
This project will be supported by industry partners Tarmac, Hanson, Imerys and Forterra, with research partners from the University College London and the University of Dundee.
Once the research project is completed, the MPA will share the results to drive adoption of this technology by cement manufacturers across the UK.
Low carbon cements and concretes represent one of seven key levers in MPA UK Concrete’s Roadmap to Beyond Net Zero. Published in 2020, the roadmap sets out the UK concrete and cement industry’s own commitments to achieving net zero, having already decarbonised by 53 percent since 1990.