Post-combustion capture is an end-of-pipe technology which captures CO2 emissions from the cement kiln.
There are many different types of post-combustion capture currently being developed. These include:
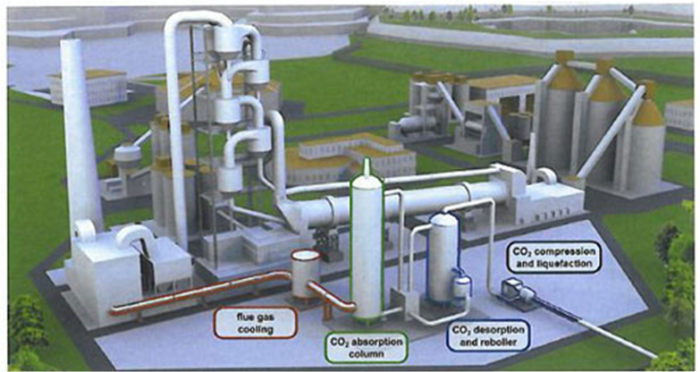
Source: ECRA
Amine-based post-combustion capture
Amine-based carbon capture is a regenerative process using an amine solvent to remove CO2 from flue gas. Reversing the reaction releases pure CO2 for capture and frees up the solvent for re-use.
Amine-based post-combustion capture (PCC) is a well-proven and commercially-available technology, having been used in the petroleum sector since 1996 and in the coal-fired power industry since 2014. In the cement industry, it was successfully used to capture carbon dioxide (CO2) during a small-scale trial at Norcem’s Brevik plant in Norway, a project that is now being scaled up to capture up to 400,000 tonnes per year of CO2.
The technology uses an amine solvent to scrub CO2 from the flue gas. The flue gas is initially fed into an absorption column, where the solvent selectively removes the CO2. The CO2-rich solvent is then fed into a desorber column, where it is heated to release the CO2, which is captured before being sent for geological storage or onward use. This regeneration process is highly energy intensive, however, posing an economic and environmental challenge.
The regenerated solvent is cooled and returned to the absorption column.
Commercially-available amine solvents can be grouped into first and second generations. First-generation solvents include mixtures of water and monoethalolamine (MEA), diethalolamine (DEA), triethanol amine (TEA) or potash. Of these, MEA is most widely used for CO2 absorbtion, due to its high selectivity, quick reaction and low cost. However, it is also sensitive to impurities and requires desulfurization and denitrification of the flue gas to work effectively.
Second-generation solvents include improved blends of sterically-hindered alkaloamines and amino acids that require lower regeneration temperatures and are more resistant to degradation. However, they cost more than and do not perform as well as MEA.
Despite the challenges, amine-based PCC is the most advanced carbon capture technology available to the cement industry with several suppliers on the market. Its planned commercial-scale deployment at Brevik – where waste heat from the cement manufacturing process will be used to optimise the process – is set to provide valuable operating experience to the industry, easing its future adoption by other cement plants.
Ammonia-based post-combustion capture
Ammonia-based carbon capture is an emerging technology using a chilled ammonia process to remove CO2 from flue gas. Trialled in the power industry, its use in the cement industry is now the subject of R&D efforts.
Ammonia-based post combustion capture (PCC) used a chilled ammonia process (CAP) to separate carbon dioxide (CO2) from flue gas. The process is relatively new, only patented in 2006, and provides a number of advantages over the more mature amine-based PCC technology, including lower costs and global availability of aqueous ammonia, higher stability in the presence of flue gas impurities, such as NOx and SOx, and lower energy requirements.
The process is similar to amine-based PCC – with the addition of a cooling step for the flue gases. After the cooler, the flue gases are sent through an absorber, where the CO2 is removed by the ammonia solution. The now CO2-rich solution then moves to the desorber, where it is heated, stripping out the CO2, which is captured and processed for transported to geological storage or onward use.
The ammonia solution can then be re-used within the system, after controlling for ammonia slip, without the need for the purging and topping-up required with amine-based solvents, which degrade over time.
The technology has been demonstrated at a pilot scale by Alstom for CO2 concentrations of between 3% and 16%, which are lower than those found in cement plant flue gas. The higher CO2 concentration of cement plant flue gas would require some changes to the process, such as higher liquid-to-gas flow rate ratio, higher ammonia concentration in the solvent, higher CO2 loading of the solvent, or a combination of these.
There is also the known possibility of clogging due to the formation of solids within the process equipment. Current CAP operations avoid this by limiting the ammonia and CO2 concentration in the absorber; however, creates challenges when it comes to system optimisation and could be a particular obstacle to implementation in the higher CO2 concentrations found in cement plant flue gases. As a result, second-generation CAP technology is designed to take advantage of and control solid formation as part of the carbon capture process. Ammonia-based PCC of CO2 does offer some competitive advantages over conventional amine-based PCC. It is however yet to be proved at commercial scale or within the flue gas conditions found in the cement industry. It also adds to health and safety challenges, due to the need for a refrigeration unit to cool the flue gas and the risk of explosion associated with the dry CO2-ammonia reaction.
Membrane-based post combustion capture
Membranes have been used for gas separation since the 1970s and are now seen as a promising technology for the removal of CO2 from cement plant flue gases.
Membrane-based gas separation is a technologically-mature process used at industrial scale since the 1970s for air separation, natural gas treatment, hydrogen purification, and the capture of pollutants. Recently, it has been recognised as a promising second-generation technology for carbon capture with a flagship demonstration project under development in the energy sector by Membrane Technology Research (MTR) in the USA.
Membrane technology uses a tailor-made material to selectively separate gases based on the permeability difference between different gaseous species. In contrast to other carbon capture technologies, steady-state operation is systematically used, with no regeneration step required. The driving force for separation is generated through a partial pressure difference between the upstream (retentate) and the downstream (permeate) side of the membrane. In low-pressure feeds, such as carbon capture, feed compression or permeate vacuum pumping is therefore required to provide the pressure differential that drives the process.
The practical application of membranes is based on numbering up (not scaling up) units with as many modules used as required in parallel – for some applications these can number into the thousands. A pre-treatment step is also usually required to remove any materials (dust, aerosols, trace organics) that could damage the membrane. The typical lifetime of a membrane is five to seven years.
Although discarded as a possible carbon capture technology for a long time, interest is picking up. Membranes offer the potential for high energy efficiency post-combustion capture of bulk concentrations of high purity (70%) carbon dioxide (CO2) from flue gases with CO2 content above 20%. When higher-purity recovery is required, hybrid processes that combine membranes with a polishing step (absorption, cryogenics) are more efficient.
The use of dedicated chemically-activated membranes have also recently been reported for carbon capture in cement production.
Membranes offer a number of promising advantages. There is no need for chemicals in the process (and therefore no chemical waste) or regeneration step. They are also a proven technology with the ability to scale up as required for industrial processes. Their application to carbon capture has thus far been limited and more work is needed before the technology is ready for commercial application.