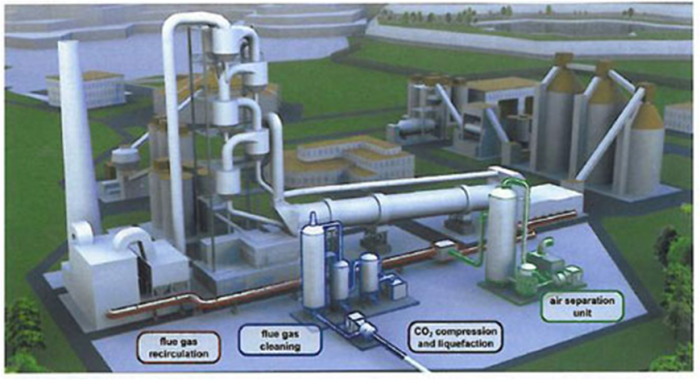
Source: ECRA
Oxyfuel combustion creates a flue gas of highly-concentrated CO2 that is relatively easy to capture and process for geological storage or onward use.
Combustion in an oxygen-rich environment – known as oxyfuel combustion – produces a flue gas of highly-concentrated carbon dioxide (CO2) that is relatively simple to process and send for geological storage or onward use. The technology has been investigated most prominently in recent years by the energy sector with various pilot and demonstration facilities built and operated.
Research within the cement industry is investigating various options for an oxyfuel clinker burning process – and its potential impact on product quality and cost. Two different approaches are under development: full oxyfuel of the complete pyroprocess or partial oxyfuel in only the raw material calcination phase.
While full oxyfuel has higher capture rates (90%-99%), it requires greater adaptation of the production line. In contrast, partial oxyfuel capture rates are lower, at 55%-75%, but only requires adaptation of part of the pyroprocess. This makes it a more economical option and presents the opportunity for staged implementation of oxyfuel technology, mitigating the capital requirements.
At the plant, oxyfuel technology requires the installation of an air separation unit (ASU) to provide the large quantities of oxygen needed to generate oxyfuel conditions, as well as a heat recovery system for the recirculation of flue gases to avoid additional firing and unabated CO2 emissions. The integration of this equipment more than doubles the amount of electricity required per tonne of clinker, raising the final cost of the production by 40%-50%.
In addition, process and equipment improvements are required to reduce false air leakage into the system. Burner/cooler design also needs adapting.
Despite this, oxyfuel remains one of the most economical candidates for CO2 capture at cement plants and is the focus of much of the sector’s research and development, with no significant technology barriers to its implementation currently identified.