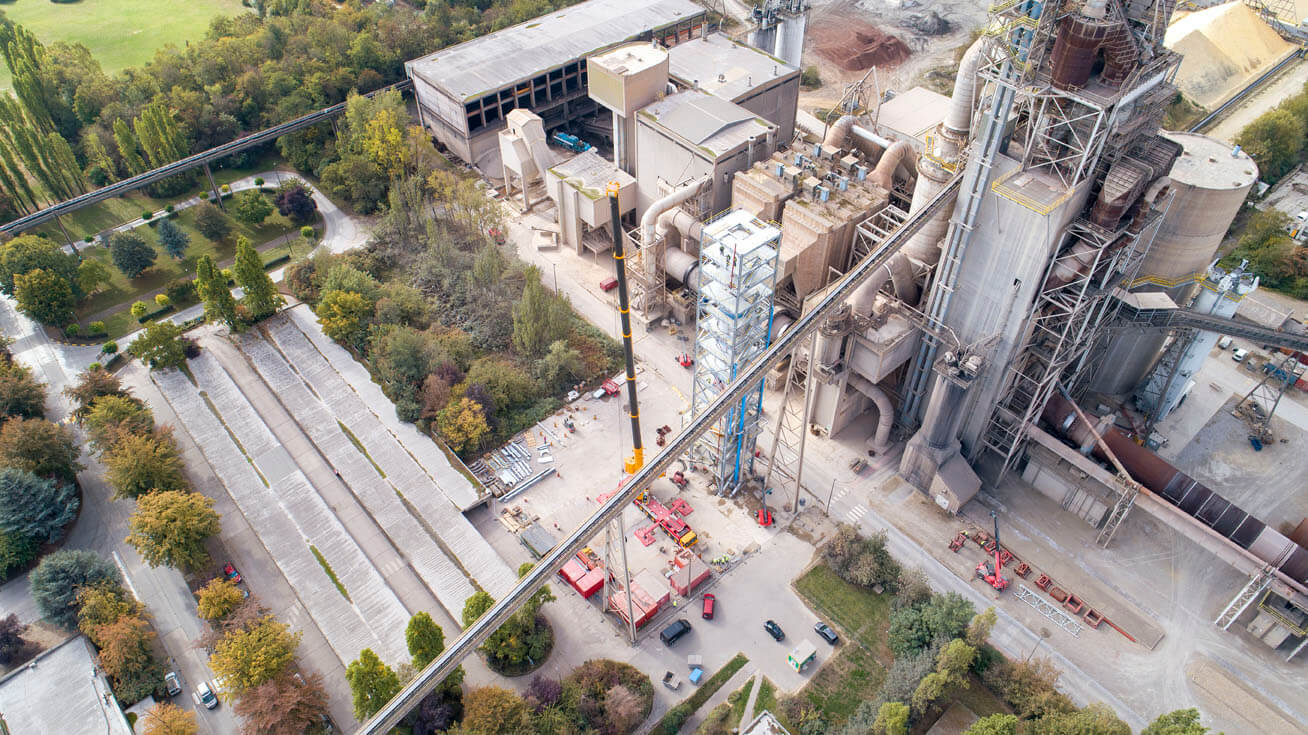
Process CO2 emissions account for two-thirds of those produced during cement manufacture. Keeping them separate through indirect calcination allows them to be more easily captured.
Direct separation – or indirect calcination – describes a set of technologies that changes the way limestone is heated during cement manufacture.
In a traditional cement plant, limestone is heated directly by the combustion of fuel in the calciner. This mixes the carbon dioxide (CO2) released by the breakdown (or calcination) of the limestone (the process emissions) with the emissions that result from the combustion of the fuel. Direct separation differs in that it heats the limestone indirectly, keeping the process emissions separate.
As these process emissions contain just CO2 and steam, the CO2 is easily captured – without need for further treatment or processing – and compressed for transport to geological storage or for onward use. Direct separation therefore offers the opportunity to capture the process emissions, which account for about two-thirds of CO2 produced by cement manufacture, without significant energy or capital costs. It is also easily adapted to current processes.
Current projects testing direct separation include LEILAC, which is based on an indirect heating method developed by Calix, and SOLPART, which uses solar energy as the heat source, rather than the combustion of traditional fuels.
Direct separation technologies can also be easily paired with other technologies, such as oxyfuel combustion, to capture the CO2 resulting from the combustion of fuel for heating, or with renewable energy sources.
These technologies are however yet to reach commercial scale development with work still required to upscale and integrate within the standard rotary kiln arrangement of cement plants. Despite this, they are a promising energy-efficient alternative to post-combustion capture technologies for the cement industry’s problematic process emissions.